Types of Animal Feed Pellets for Poultry
The production of animal feed pellets using a pellet making machine for poultry feed encompasses various types that cater to the unique dietary needs of different poultry species such as chickens, ducks, turkeys, and more. These feed pellets are formulated using diverse ingredients to furnish balanced nutrition, ensuring optimal growth and health of the poultry.
For chickens, feed pellets generally include a mixture of grains like corn, wheat, and barley along with protein-rich sources such as soybean meal, fish meal, and meat meal. Additionally, vitamins and minerals are integrated to supply essential nutrients that foster egg production and enhance overall health. Ducks, on the other hand, benefit from a diet high in protein and low in carbohydrates. Their feed pellets often comprise corn, peas, rice bran, and sunflower meal, supplemented by inessential amino acids and vitamins to sustain their rapid growth and health.
Turkeys require a high-calorie diet rich in protein to support their larger size and rapid growth rate. Thus, turkey feed pellets are typically formulated with a higher concentration of protein sources like soybean meal, fish meal, and canola meal. Also, grains such as corn and sorghum along with added vitamins and minerals ensure their robust health and development. Other poultry species such as quails and geese have specific nutritional needs tailored in their feed pellets to match their distinct growth patterns and health requisites.
Emphasizing the precise formulation of feed pellets is vital to meet the particular dietary necessities of each poultry type. RICHIE’s pellet making machine for poultry feed facilitates the production of high-quality feed pellets, enhancing the efficiency of nutrient delivery and digestion for various poultry types. As a result, well-formulated feed pellets contribute significantly to the healthy growth, productivity, and overall wellbeing of poultry, underscoring the importance of precision in feed manufacture.
Advantages of Poultry Feed Pellets
Poultry feed pellets have garnered significant attention within the farming community due to their numerous advantages over traditional feed forms. One notable benefit is the improvement in feed efficiency. When utilizing a pellet making machine for poultry feed, the uniformity of the pellets ensures that each bird receives a balanced diet, which promotes overall nutrient absorption. Unlike loose feeds, pellets are designed to be nutritionally complete, thus ensuring the poultry ingest all necessary vitamins and minerals.
Furthermore, feed pellets significantly reduce feed wastage. Traditional feed forms, such as mash or crumble, often lead to spillage and degradation. In contrast, pellets are less susceptible to disintegration, which means more feed ends up being consumed rather than wasted. This reduction in waste directly correlates to cost savings for poultry farmers and a more efficient feeding process.
Handling and managing feed is also vastly improved when using pellets. The compact and uniform nature of feed pellets allows for easier storage, transportation, and automated feeding, thereby reducing labor and improving logistics. Pellets minimize the dust problems associated with powdered feeds, leading to a cleaner feeding environment and reducing respiratory issues for both poultry and handlers.
Selective feeding behaviors, wherein poultry pick and choose what they eat from mixed feeds, can lead to nutritional imbalances and decreased productivity. Pellets mitigate this issue by combining all necessary nutrients into a single, consumable product. This holistic approach ensures that the poultry consistently consume a well-rounded diet, boosting their health and productivity.
In addition, incorporating a pellet making machine for poultry feed into the production process plays a crucial role in enhancing food safety. The high-temperature processing involved in pellet formation can destroy harmful pathogens, ensuring that the final product is safe for consumption. Consequently, poultry raised on pellet feeds often exhibit better overall health, leading to increased production rates and higher-quality outputs.
Overview of RICHI Pellet Making Machines for Poultry Feed
RICHI’s range of pellet making machine for poultry feed production is meticulously designed to cater to diverse production needs, from small-scale farm operations to large industrial feed mills. Each model in their lineup boasts a unique set of features and capabilities, ensuring that producers can find the optimal solution for their specific requirements.
The range includes various models such as the SZLH series, which spans from smaller machines capable of producing 1-2 tons per hour, to larger units that can deliver up to 20 tons per hour. Smaller models are ideal for farms or localized production, while the high-capacity machines serve large-scale commercial operations that necessitate continuous, efficient output.
One of the defining characteristics of RICHI pellet making machines is their adaptability. The machinery is built to handle different feed formulations, making it easy to switch between recipes without compromising the quality of the pellets. This flexibility is particularly beneficial for producers who need to tailor feed compositions based on the nutritional requirements of different poultry species or growth stages.
Moreover, RICHI pellet making machines are equipped with advanced features that enhance production efficiency and product quality. These include robust pellet dies and rollers, high-precision electric motors, and sophisticated control systems that allow real-time monitoring and adjustments. Such features contribute to producing uniform, high-quality pellets that meet industry standards.
RICHI machines also stand out due to their energy efficiency and durability. The design focuses on minimizing energy consumption while maintaining consistent performance, thus offering cost savings on operational expenses. Additionally, the machines are built with high-quality materials and components, ensuring longevity and reliability under continuous usage.
Overall, RICHI pellet making machines are trusted by poultry feed producers worldwide for their capacity, versatility, and technological advancements. By investing in RICHI machinery, producers can enhance production efficiency, maintain high-quality feed standards, and adapt to the evolving demands of the poultry industry.
Working Principle of Ring Die Poultry Feed Pellet Machine
The ring die poultry feed pellet machine is central to efficient feed production. It operates through a sequence of well-orchestrated steps, starting with material preparation. Raw materials, including grains, such as corn or wheat, and additives, are ground into a fine powder to ensure uniformity in texture, which is crucial for the pelletizing process.
The prepared material is then directed to the feeder, which regulates the flow into the ring die chamber. The feeder ensures a consistent and controlled supply of the material, a critical factor for maintaining quality and production efficiency. In the die chamber, the material moves towards the rollers, which play a vital role in compressing the material against the inner surface of the ring die.
The ring die, characterized by its circular structure embedded with perforations, receives the material under high pressure exerted by the rollers. This process forces the material through the die holes, transforming the finely ground powder into solid pellets. The design and diameter of the die holes are decisive factors that determine the size and density of the poultry feed pellets.
Conditioning is another essential stage in this process. During conditioning, steam and water may be added to elicit a gelatinization effect, enhancing the nutritional value and digestibility of the feed pellets. This stage also ensures the material is sufficiently pliable for effective pellet formation.
Once the pellets exit the ring die, they are still hot and soft, necessitating a cooling phase. The cooling process solidifies the pellets and reduces their temperature to prevent spoilage and maintain product integrity. Efficient cooling preserves the structural quality of the pellets, making them easier to handle and store.
In conclusion, the ring die poultry feed pellet machine integrates several complex components and processes. From material preparation and conditioning to pelletizing and cooling, each step is critical for producing high-quality poultry feed. Understanding this working principle helps in optimizing the use of pellet making machines for poultry feed, ultimately leading to better feed quality and efficiency in poultry farming.
Characteristics of RICHI Pellet Making Machines for Poultry Feed
RICHI pellet making machines for poultry feed are renowned for their distinctive features and advanced technical specifications, setting them apart as industry leaders. One of the key attributes of these machines is their exceptional durability. Constructed from high-grade materials, these pellet making machines are designed for long-term use, enduring the rigorous demands of continuous operation in various conditions.
Energy efficiency is another standout feature of RICHI pellet making machines. These machines are engineered to consume less power while maintaining high productivity levels. This not only reduces operational costs but also minimizes the environmental impact, making them a sustainable choice for poultry feed production.
The ease of operation and maintenance further enhances the appeal of RICHI pellet making machines. The user-friendly design ensures that even operators with minimal training can efficiently manage the machine, reducing the need for extensive labor and specialized skills. Additionally, routine maintenance is simplified through accessible machine components and clear instructions, thereby decreasing downtime and enhancing overall productivity.
Advanced technological aspects are integral to the superior performance of these machines. RICHI pellet making machines are equipped with cutting-edge automation and control systems. These features enable precise regulation of pellet size, moisture content, and feed formulation, ensuring consistent quality. The automation also facilitates streamlined production processes, reducing human error and optimizing efficiency.
Safety features are meticulously integrated into RICHI pellet making machines to protect operators and ensure safe operation. These machines incorporate comprehensive safety systems, including emergency stop buttons, overload protection, and robust guarding mechanisms. These safety measures not only protect operators but also prolong the lifespan of the machine by preventing damage and wear.
In conclusion, RICHI pellet making machines for poultry feed stand out due to their durability, energy efficiency, ease of operation, advanced technological features, and stringent safety protocols. These characteristics collectively contribute to their high performance and reliability in the poultry feed production industry.
Production Process of Poultry Feed Pellets
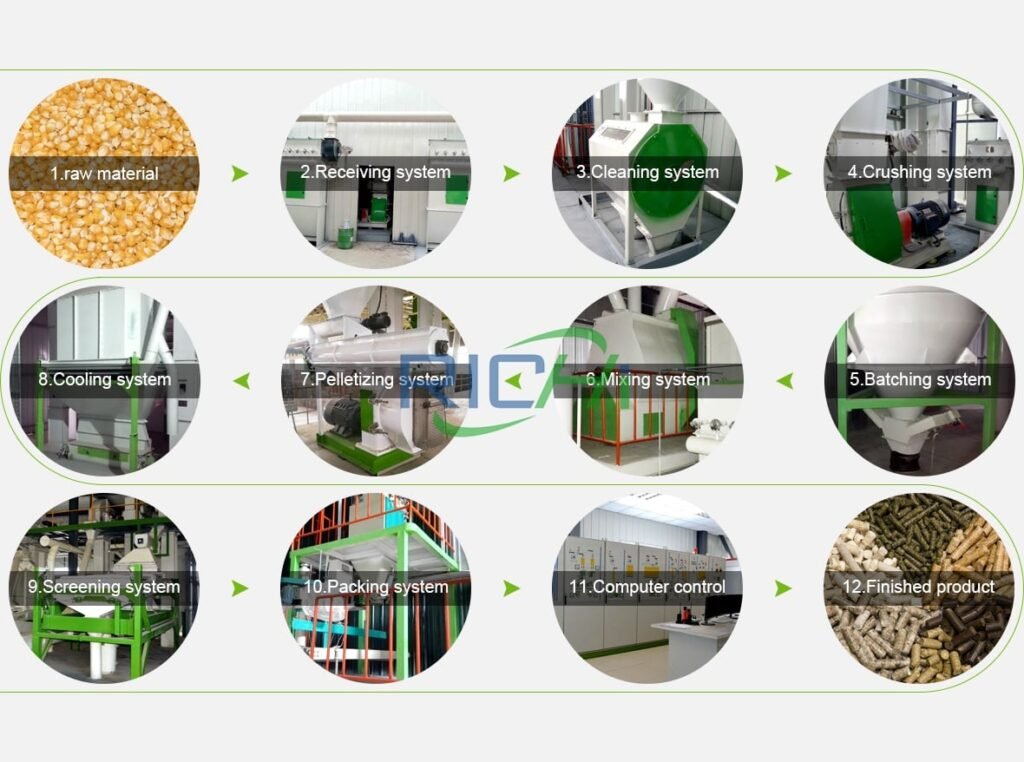
The production of poultry feed pellets using a pellet making machine for poultry feed involves a meticulous series of steps designed to ensure both nutritional integrity and physical quality. The initial stage, raw material selection, is critical. High-quality ingredients, such as grains, protein sources, vitamins, and minerals, are chosen based on the specific dietary needs of poultry.
Subsequently, these raw materials undergo grinding. This process reduces the particle size, improving the homogeneity of the feed mixture and facilitating efficient digestion by poultry. The finely ground materials are then subjected to mixing, where a uniform distribution of all ingredients is achieved. This homogeneity is crucial for delivering consistent nutrition in every pellet.
The next stage is conditioning. The mixed feed is treated with steam to raise its temperature and moisture content. This not only softens the feed but also aids in killing any potential pathogens, thereby enhancing both the quality and safety of the final product. This preparatory step is essential before the feed enters the pelletizing phase.
Pelletizing is where the magic happens. The conditioned feed is pressed through a pellet die using the pellet making machine for poultry feed. This compresses the mixture into firm, uniform pellets. The strength and durability of these pellets are vital, as they need to withstand handling and transportation without disintegrating.
Post-pelletizing, the hot, moist pellets are too fragile for immediate use. Thus, they are transferred to a cooling system. This stage involves reducing the temperature and moisture content of the pellets, which solidifies them and ensures they maintain their shape and integrity. Proper cooling is essential for preventing mold growth and prolonging the shelf life of the feed.
The final step is packaging. The cooled pellets are carefully weighed and packed into bags or bulk containers, ready for distribution. This step involves ensuring that the packaging is secure to protect the feed from environmental factors such as moisture and contaminants. The core objective here is to deliver high-quality poultry feed that meets the nutritional requirements while maintaining its physical form from the factory to the farm.
Additional Equipment Needed for Poultry Feed Line
The production of poultry feed pellets necessitates a variety of equipment beyond the pellet making machine for poultry feed. This section will explore the essential pieces of equipment required to complete a comprehensive poultry feed production line.
First and foremost, mixers play a vital role in ensuring uniformity and consistency in the feed mixture. Their primary function is to blend different raw materials thoroughly, allowing for the even distribution of nutrients throughout the poultry feed. Achieving a homogeneous mix is crucial in maintaining the nutritional quality that meets the dietary requirements of poultry.
Grinders, or hammer mills, are another key component in the feed production line. These machines are responsible for reducing raw material particle size, facilitating easier blending and subsequent processing. Fine grinding ensures that the feed ingredients are adequately prepared for efficient pelletization, enhancing the overall feed structure and palatability.
Conditioners are also indispensable in the poultry feed production process. Essentially, they prepare the feed mixture by adding moisture and heat, which softens the materials and prepares them for optimal pellet formation. Conditioning enhances the binding properties of the feed, ensuring pellets are dense, durable, and have a desirable texture and uniform nutrient profile.
After conditioning, the cooled feed is passed through coolers. Cooling is crucial to the pelletizing process because it reduces the temperature and moisture content of the fresh pellets. This stabilization step helps in preserving the quality of the feed, preventing mold growth and degradation of nutrients during storage.
Lastly, packaging machines are essential at the end of the production line. Once the feed pellets are produced and cooled, they must be properly packed for distribution. Efficient packaging machines ensure that the feed is securely contained, minimizing exposure to air and contaminants, thus safeguarding the feed’s quality until it reaches the end-user.
In combination with the pellet making machine for poultry feed, these additional pieces of equipment create an integrated and efficient production line that ensures high-quality feed suitable for various poultry livestock. Each machine plays a crucial role, collectively contributing to a streamlined and effective feed production process.
Reasons to Choose RICHI Equipment
When selecting a pellet making machine for poultry feed, it is crucial to choose a manufacturer known for its reliability, innovation, and excellent customer support. RICHI stands out as a leading industry provider due to its stellar reputation and proven track record in delivering high-performance machinery. The company is synonymous with quality and efficiency, making it a preferred choice among poultry feed producers worldwide.
RICHI’s commitment to innovation is evident in its cutting-edge designs and technological advancements. Each pellet making machine is crafted with precision engineering to ensure durability and operational efficiency. These machines are designed to maximize production output while minimizing energy consumption, essential for cost-effective and sustainable feed production. The integration of advanced features and automation systems simplifies the pelletizing process, enabling producers to achieve consistent, high-quality pellets effortlessly.
Another strong reason to opt for RICHI equipment is the impeccable customer support services they offer. From initial consultation to after-sales support, RICHI provides comprehensive guidance and assistance to ensure optimal machine performance. Their technical team is readily available to address any issues, offering solutions that enhance the overall user experience. This ensures that poultry feed producers can rely on uninterrupted production, thereby maintaining supply chain efficiency.
The value for money RICHI provides is unrivaled. Investing in a RICHI pellet making machine ensures long-term savings through reduced maintenance costs, lower energy consumption, and increased productivity. The company also offers customizable solutions tailored to the specific needs of each producer, thereby delivering not only high-quality equipment but also excellent value.
Testimonials from satisfied customers further exemplify the advantages of choosing RICHI. Many users have reported significant improvements in production efficiency and pellet quality after integrating RICHI machines into their operations. Case studies highlight how RICHI’s equipment has become an integral part of successful poultry feed production systems, solidifying the company’s position as an industry leader.