Introduction to Animal Feed Pellet Mill Machines
An animal feed pellet mill machine is a pivotal tool utilized in the agricultural sector, designed to convert raw feed ingredients into compact, digestible, and convenient pellet form. These machines essentially take raw materials such as grains, soybean meal, maize, and other nutritional elements, compressing them into uniform pellets. This transformation is crucial for enhancing feed efficiency by facilitating easier handling, precise dietary formulation, and consistent nutrient distribution.
The fundamental role of an animal feed pellet mill machine extends beyond mere conversion of feed ingredients. It plays a critical part in modern animal farming practices, where optimal nutrition is key to maintaining healthy livestock and maximizing production. By ensuring a homogeneous mix of ingredients, feed pellets provide animals with consistent nutrients in each meal, leading to improved growth rates, better feed utilization, and overall enhanced animal health.
Moreover, the production of feed in pellet form addresses several logistical challenges. Pellets are denser and more compact than their loose or mash counterparts, which significantly reduces storage space requirements and minimizes losses due to dust or spoilage. This aspect is particularly beneficial for large-scale farming operations, where space efficiency and feed preservation are of paramount importance. Additionally, the uniformity of pellets ensures ease of transportation and mechanical handling, resulting in reduced labor costs and minimized feed wastage.
In modern industry settings, the importance of animal feed pellet mill machines cannot be overstated. They are indispensable for facilitating high-quality, consistent, and efficient feed production, directly contributing to more sustainable and profitable farming practices. As such, these machines represent a significant advancement in the field of animal agriculture, underscoring their critical role in meeting the growing demands for animal feed in an increasingly resource-conscious world.
Animal feed pellet mill machines play a crucial role in the agricultural and livestock industries, providing versatile applications tailored to various animal types. These machines serve a broad spectrum of livestock including poultry, cattle, fish, and pets, effectively addressing their unique dietary requirements and feeding practices.
Poultry
In the poultry sector, feed pellet mill machines are instrumental in producing nutritionally balanced pellets that promote optimal growth and health. The machines are capable of blending grains, proteins, vitamins, and minerals in precise proportions, ensuring that chickens receive feed that supports egg production, weight gain, and overall vitality. The uniform pellet size also reduces waste, as poultry are less likely to scatter or avoid smaller, unpalatable feed particles.
Cattle
For cattle, these machines transform raw materials into compact, digestible pellets that are easier to store, handle, and measure. Cattle feed pellets often include a mix of grains, forage, and supplements designed to enhance milk production in dairy cows or promote muscle growth in beef cattle. The use of feed pellet mills ensures the consistency and quality of the feed, which is critical for maintaining the health and productivity of the herd. Related: https://www.richimanufacture.com/cattle-feed-plant-machine/
Fish
In aquaculture, animal feed pellet mill machines offer a tailored solution for producing floating or sinking pellets suitable for different fish species. Fish feed pellets are formulated to meet the specific nutritional needs of freshwater and marine fish, providing essential nutrients that aid in rapid growth, disease resistance, and efficient feed conversion. The customized feed shapes and sizes also improve water quality by minimizing feed particles that can degrade and pollute aquatic environments.
Pets
Pet owners and manufacturers also benefit from animal feed pellet mill machines, which produce high-quality pet food pellets. These machines can create a variety of pelletized feeds using ingredients that cater to different dietary needs and preferences. For instance, dog food pellets may include meat, grains, and vegetables to support energy and health, while cat food pellets might be richer in proteins and fats to match their metabolism. The process ensures that pets receive nutritionally balanced meals in a convenient, easy-to-consume form.
Overall, the applications of animal feed pellet mill machines are diverse and indispensable across the livestock and pet food industries, contributing to the well-being and productivity of various animal categories through customized, high-quality feed solutions.
Components of Animal Feed Pellet Production Line
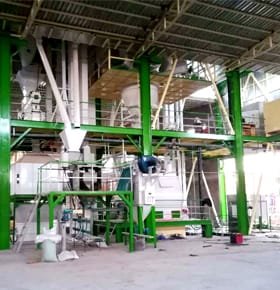
The production of high-quality animal feed pellets necessitates a well-coordinated sequence of processes, each critical to achieving the desired nutritional and physical properties. The animal feed pellet production line is a comprehensive system composed of several integral components, each playing a pivotal role. Understanding these elements can enhance the efficiency and output of an animal feed pellet mill machine. Related: https://www.richimanufacture.com/animal-feed-pellet-plant/
1. Mixing: The process begins with mixing, where various raw ingredients such as grains, vitamins, and minerals are combined. This step ensures a uniform distribution of nutrients throughout the feed. Precision in mixing is crucial to maintain consistency and quality in the final product.
2. Grinding: Post-mixing, the feed mixture undergoes grinding. This involves reducing the particle size of the raw materials to a fine consistency, facilitating easier processing and better digestibility for the animals. The grinding process helps in achieving the right texture for the pelletizing stage.
3. Conditioning: Here, the ground feed is subjected to moisture and heat in controlled conditions. Conditioning improves the binding quality of the feed particles, making them more pliable and enhancing the effectiveness of the subsequent pelletizing process. It also helps in eliminating pathogens, thus ensuring feed safety.
4. Pelletizing: This is the core function of the animal feed pellet mill machine. The conditioned feed is pressed through a die, transforming it into pellet form. The machinery’s precision in this stage is paramount as it determines the size, shape, and density of the pellets, directly impacting the feed’s palatability and nutritional value.
5. Cooling: The newly formed pellets are hot and need to be cooled down to room temperature. Cooling solidifies the pellets, reducing moisture content and improving storage stability. It is a critical step to prevent the degradation of the feed and to maintain pellet integrity.
6. Screening: After cooling, the pellets undergo screening to remove any fine particles or oversized pellets. This quality control step ensures that only uniformly sized pellets proceed to the final stage, optimizing feed quality and minimizing waste.
7. Packaging: The final stage involves packaging the screened pellets for storage and transportation. Proper packaging protects the feed from environmental factors such as moisture and contamination, ensuring they remain in optimal condition until they are used.
Each component of the animal feed pellet production line is vital to producing a high-quality product. By paying attention to these details, operators can maximize the efficiency and effectiveness of the animal feed pellet mill machine.
Role of the Pellet Mill Machine in the Production Line
Within the vast and intricate animal feed production line, the animal feed pellet mill machine occupies a pivotal position. This machine sits strategically between the conditioning and cooling phases, fundamentally determining the quality and consistency of the feed. Post the conditioning phase, where raw feed ingredients are mixed and steam added to achieve the proper texture and moisture, the feed is routed to the pellet mill machine for further processing.
The core function of the animal feed pellet mill machine is to compress the conditioned feed material into uniform pellets. This is achieved through a dye and roller system, which applies mechanical pressure to shape the feed into cylindrical pellets. The die specifications and pressure settings are meticulously calibrated to ensure that the feed pellets produced meet predefined standards of size and density, thereby ensuring that every batch maintains consistent physical characteristics.
The size and density of the pellets produced are crucial for several reasons. Uniform feed pellets ensure that animals receive the appropriate quantity of nutrients in each portion, preventing irregular feed intake and promoting better health and growth. Furthermore, consistent pellet size facilitates more efficient storage and transportation, as well as ease of handling during feeding.
Following the pelletizing process, these newly formed pellets are relatively warm and often possess higher moisture content. To stabilize them, the next stage involves passing the pellets through a cooling phase. Coolers lower the temperature and moisture to ambient conditions, solidifying the pellets and making them ready for storage and transportation. Hence, the precision and efficiency of the pellet mill machine directly impact the overall effectiveness and quality of the feed production line. Through its critical intermediary role, the animal feed pellet mill machine ensures the feed advances seamlessly from conditioning to a thoroughly stable product ready for consumption.
Detailed Features of Animal Feed Pellet Mill Machines
Modern animal feed pellet mill machines are designed with numerous advanced features that significantly enhance their performance and durability. One of the most notable features is the high build quality, which ensures long-lasting and reliable operation. The machines are typically constructed from robust stainless steel, optimizing their resistance to wear and tear, and extending their operational lifespan.
Ease of operation is another critical feature. Contemporary pellet mill machines often boast user-friendly interfaces and intuitive control systems, allowing operators to manage settings quickly and efficiently. These machines usually come with automated feeding and cutting systems, minimizing manual intervention and ensuring consistent pellet quality. The integration of advanced control systems not only enhances the machine’s efficiency but also allows for real-time monitoring and adjustment of operational parameters.
Efficiency is further complemented by the use of various die types. The dies, crucial components in pellet mills, are available in different configurations to suit specific feed requirements. The selection ranges from flat dies to ring dies, each designed to yield optimal pellet quality and production throughput. High precision in die manufacturing ensures uniform pellet size and shape, contributing to better feed conversion rates for animals.
Energy consumption is a key consideration in the design of these machines. Modern animal feed pellet mill machines are engineered to be energy-efficient, reducing operational costs while maintaining high productivity levels. Innovations such as variable frequency drives (VFDs) allow for precise control of motor speed and energy usage, further enhancing the machine’s efficacy.
Automation and control systems in state-of-the-art pellet mill machines include programmable logic controllers (PLCs) and human-machine interfaces (HMIs). These technologies automate various aspects of the pellet production process, from ingredient mixing to pellet cooling, ensuring consistency and quality in every batch produced. Additionally, some advanced models feature remote monitoring capabilities, allowing operators to supervise and control operations from a distance.
Innovative technologies like heat treatment and alloying in the machine components add to the performance and longevity of the pellet mills. Such advancements help in reducing maintenance needs and increasing the overall productivity of the animal feed pellet mill machine.
Maintenance Tips for Richi Ring Die Animal Feed Pellet Mill Machine
The longevity and performance efficiency of your Richi ring die animal feed pellet mill machine largely depend on diligent maintenance practices. A well-maintained machine ensures consistent production quality and minimizes downtime caused by mechanical failures. Here are key maintenance tips to keep your pellet mill running smoothly.
Firstly, regular cleaning routines are imperative. Accumulated feed particles and dust can adversely impact the machine’s efficiency. It is recommended to clean the machine after every batch to remove residues that could cause blockages or contamination. Pay special attention to the die and rollers as these are critical components that require unobstructed movement.
Inspection procedures are equally important. Conduct comprehensive checks periodically to identify any signs of wear or damage. Inspect the die, rollers, and bearings for cracks, excessive wear, or misalignment. It is advisable to perform a thorough inspection monthly, with visual checks conducted more frequently, especially after intensive use of the animal feed pellet mill machine.
Replacing worn-out parts in a timely manner can prevent more significant mechanical issues. The die and rollers are subject to high pressure and friction, leading to wear over time. Keep a record of the operational hours and replace these components as recommended by the manufacturer. Regular renewal of these parts ensures optimal pellet quality and production efficiency.
Lubrication schedules form a crucial part of maintenance. Proper lubrication of the rollers and bearings reduces friction and minimizes wear and tear. Develop a lubrication routine based on the manufacturer’s guidelines, ensuring that you use the recommended lubricants. Over-lubrication can be as harmful as under-lubrication, so follow the prescribed quantities and intervals.
Lastly, troubleshooting common issues can save time and resources. Familiarize yourself with the machine’s manual to understand typical problems and their solutions. For instance, inconsistent pellet size could indicate roller misalignment or a clogged die, both of which are relatively straightforward to address with routine checks.
Adhering to these maintenance tips will significantly extend the service life of your Richi ring die animal feed pellet mill machine, maintain its performance at optimum levels, and ensure the consistent production of high-quality feed pellets.
About Richi Machinery
Richi Machinery stands prominently as a vital player in the animal feed industry, renowned for its unwavering commitment to excellence and innovation. Established in the early 21st century, the company has diligently built a reputation grounded in quality, reliability, and technological advancement. The historical journey of Richi Machinery is marked by continuous growth and adaptation to the evolving needs of the animal feed production sector.
The company’s mission is clear and ambitious: to revolutionize the animal feed industry by providing cutting-edge solutions that enhance productivity and quality. At the heart of Richi Machinery’s offerings is the animal feed pellet mill machine, an innovative product designed to streamline and optimize the feed production process. Their product range is extensive, catering to diverse needs with state-of-the-art machinery capable of producing high-quality feed pellets from various raw materials.
Richi Machinery’s commitment to quality is evident in every aspect of their operation. They employ rigorous testing and quality control measures to ensure each machine meets stringent industry standards. This dedication extends to their customer service, where they provide comprehensive support and training to maximize the efficiency and longevity of their equipment.
One of the unique selling points of Richi Machinery is their focus on innovation. They continuously invest in research and development, exploring new technologies and methodologies to stay ahead in the competitive landscape. This commitment to innovation is not just about keeping pace with industry trends but setting them, as evident in their advanced feed pellet mill machines.
Success stories abound, with numerous clients experiencing significant enhancements in their feed production processes. Testimonials highlight improved feed quality, increased production efficiency, and substantial cost savings. These success stories are a testament to Richi Machinery’s influence and dedication to advancing the animal feed industry.
Conclusion
Understanding the intricacies of animal feed pellet mill machines is crucial for anyone engaged in feed production. These machines transform raw agricultural materials into high-quality, nutritious feed pellets, which are essential for the optimal growth and health of livestock. The blog has delved into various aspects of these machines, including their uses in homogenizing and enhancing feed quality, the detailed production process from raw materials to finished pellets, their critical features such as energy efficiency and durability, and the importance of regular maintenance to ensure long-term functionality.
An in-depth comprehension of animal feed pellet mill machines enables producers to make informed decisions, ultimately leading to improved productivity and reduced operational costs. High-quality feed pellets not only meet nutritional standards but also ensure better livestock performance, which is paramount in the competitive field of animal husbandry. This is where the expertise and advanced technologies of Richi Machinery come into play. With years of experience and a proven track record in the industry, Richi Machinery stands out as a reliable partner, offering state-of-the-art animal feed pellet mill machines that cater to various production needs.
In conclusion, the significance of utilizing advanced feed pellet mill machines cannot be overstated. They play a pivotal role in the efficiency and efficacy of feed production, ensuring that animals receive the best nutrition possible. By considering manufacturers like Richi Machinery, producers can benefit from machines that are designed to optimize feed quality and production efficiency, paving the way for sustainable and profitable farming practices.